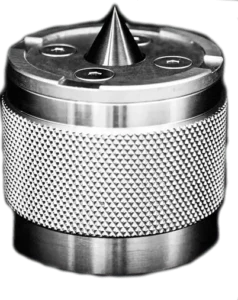
industry standard.
Founded in 1984, HUBBS is the original and most trusted manufacturer of quality targeting, accessories, and tooling components. Our designs and part numbers are recognized as the industry standard.
When precision is non-negotiable, trust HUBBS to deliver the most reliable and accurate metrology measuring equipment in the industry. Designed specifically for large-scale applications, our equipment meets the rigorous demands of several different types of industries.
Our client list now totals more than 1,700 clients in over 48 countries. This client list reads like the “Who’s Who” in industries such as aerospace, shipbuilding, and automotive. You can find our products associated with leading applied science and research laboratories around the world. From spacecraft to nuclear power, we can help with your close tolerance measuring project.
Our metrology measuring equipment sets the industry standard through advanced engineering and seamless integration, enabling you to handle the most complex projects with confidence. With our 3D metrology tooling. this equipment offers consistent performance and unmatched accuracy, safeguarding the integrity of your operations.
At HUBBS, every product reflects our commitment to quality and trust. Backed by decades of expertise, we empower professionals to excel in their fields. Elevate your measurement capabilities today. Contact us to equip your team with the precision tools they need to succeed.
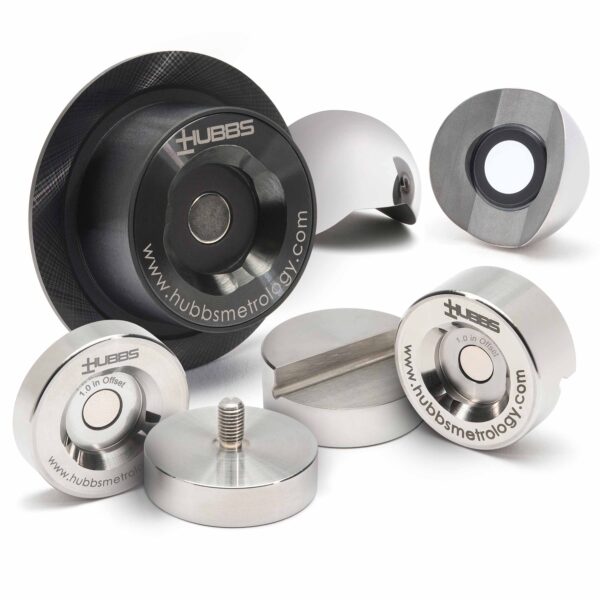
Founded in 1984, HUBBS is the original and most trusted manufacturer of quality targeting, accessories, and tooling components. Our designs and part numbers are recognized as the industry standard.
Our client list now totals more than 1700 clients in over 48 countries. This client list reads like the “Who’s Who” in industries such as aerospace, shipbuilding, and automotive. You can find our products associated with leading applied science and research laboratories around the world. From spacecraft to nuclear power, we can help with your close tolerance measuring project.
FEATURED PRODUCTS
Black Knight Enterprises, LLC
dba HUBBS Machine & Manufacturing
is ISO 9001:2015 Quality Management System Certified